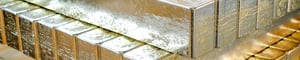
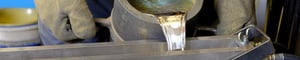
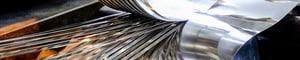
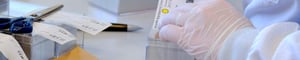
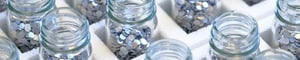
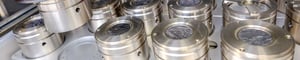
OUR KEY STRENGTHS
Years of experience, wide-ranging products and extensive know-how
The core capability of PFARR Stanztechnik lies in the manufacture of high-purity solder, braze and special alloys including Lead-free compositions. Since almost every alloy has been produced in-house for decades, our production is based on a wealth of experience in all things metallurgical. The secondary processes to convert these pure materials into high-end strip, foil, laminates and preforms calls for further advanced know-how. The synergic strength at work in our company is rounded off by the ability to transfer processes to alternative materials and the final product optimisation to suit the manufacturing processes of our customers.
Alloying
Whichever alloy you might be looking for, purity is our guiding principle. Our melting processes start with high-purity metals (generally minimum 99,99 %), because even tiny impurities can reduce the wettability of a solder. Nummerous PFARR solders are deployed flux-free under reducing atmospheres or under vacuum.
Using diverse melting techniques we are able to offer a wide production spectrum. The enormous range of elements used in our melts range from Sn, Pb, Ag, Au, Ni, Co, Cu, Pd, In, Sb, Bi, through rare earths to metalloids like Ge.
PFARR Stanztechnik alloys and dopes to individual customer requirements. If you wish you can choose every detail ofan alloy you require. Though, of course, you are also free to call on our wide range of regularly produced alloys. List of alloys
Our technical material support staff can help you in choosing suitable alloys: SALES
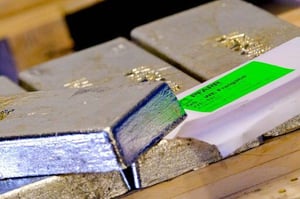
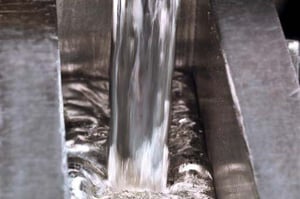
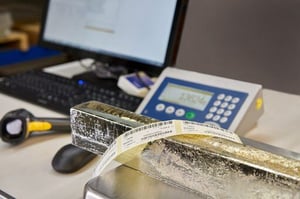
Rolling
High precision stamped and stamped-formed components can only be produced from high-tech intermediate strip. At PFARR Stanztechnik we have a wide range of rolling techniques and equipment available to match the diverse range of materials and strip geometries in use.
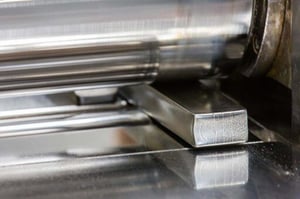

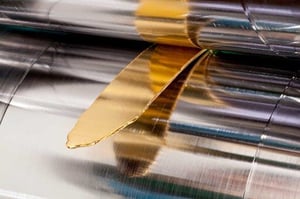
Cladding
Metallurgically, cladding refers to single or double-sided lamination of a carrier material with a secondary metal skin. A careful combination of pressure and simultaneous plastic deformation results in a complete physical bond between the metal surfaces. Such laminated materials combine the specific advantages of the materials deployed. Classical flat rolling of large amounts of material with a continuous coating thickness is an economic production route.
In contrast to alternative thin layer coating techniques such as chemical and physical vapour deposition and plating processes, cladding enables much thicker skins to be produced. What’s more, problematic material combinations in melting and alloying techniques can be readily addressed.
Each customer requirement is individually developed. Speak to our material support specialists: SALES
Stamping and cutting
Stamping is our strongest suit. We stamp and cut at high precision with minimal tolerances. This holds true whether the parts in question are simple (discs, squares, washers), complex stamped profiled components, deep drawn parts or narrow strips cut from rolls.
Materials | Non-ferrous metals, bimetallics, plastics, laminates |
Strip thicknesses | from 0.02 mm to 5 mm |
Strip width: | max. 180 mm |
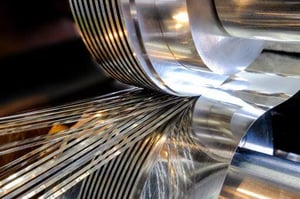
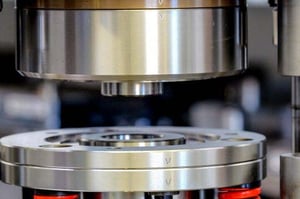
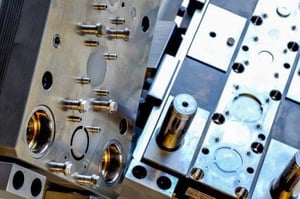
Packing
To eliminate oxidation issues, we recommend packing your preforms in daily-usage quantities; perhaps under a protective atmosphere. Depending on the particular product concerned, we then generally offer a guaranteed shelf-life – if stored properly. We pack in every container available on the market: glass jars, poly bags, bottles, in rolls or on spools; whatever your needs might be.
Tape and reel blister packs to DIN EN 60286-3:2014-02
Blister packs offer particularly good protection to components, as well as making for easy automated production processes. Our packaging line can handle components with edge lengths of up to 60 mm; if required in ESD [electrostatic discharge] anti-static plastic materials. Each cavity is hot-sealed with a plastic cover foil. The tape widths can vary between 8 and 72 mm. To provide for safe transportation, filled tapes, wound onto plastic reels, are further sealed in poly bags.
Type | Procedure | Advantages |
Loose packed | manual or semi-automated | Economical, for non-critical product requirements |
Stacked | manual or semi-automated | Excellent cost-benefit, for higher product demands |
Waffle pack | semi-automated | Optimum solution for high product requirements |
Tape and reel | Fully automated | The best solution for fully automated assembly lines |
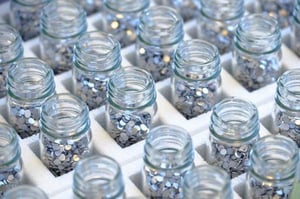
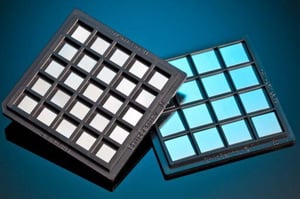
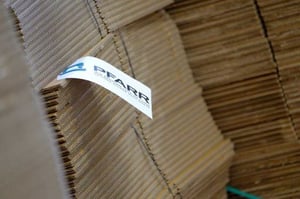